

This function essentially gives you the number of milliseconds passed since the start of the program. we can keep track of the current time we can compute the delta time by subtracting the current time from the previous time now to get the updated control signal every t seconds. Now in order to make sure that we get a uniform interval of sample time t we first start off by storing the current time the program has been running by using a built in function in Arduino IDE called millies. Now just to make things easier I kept the computation of the control signal in a separate function called the control. This is needed because it allows more precise computation. And you’ll notice most of these are of the double data type or floating point. I’ll now proceed to explain the code line by line. So first we start off by defining a variables needed for the computation.
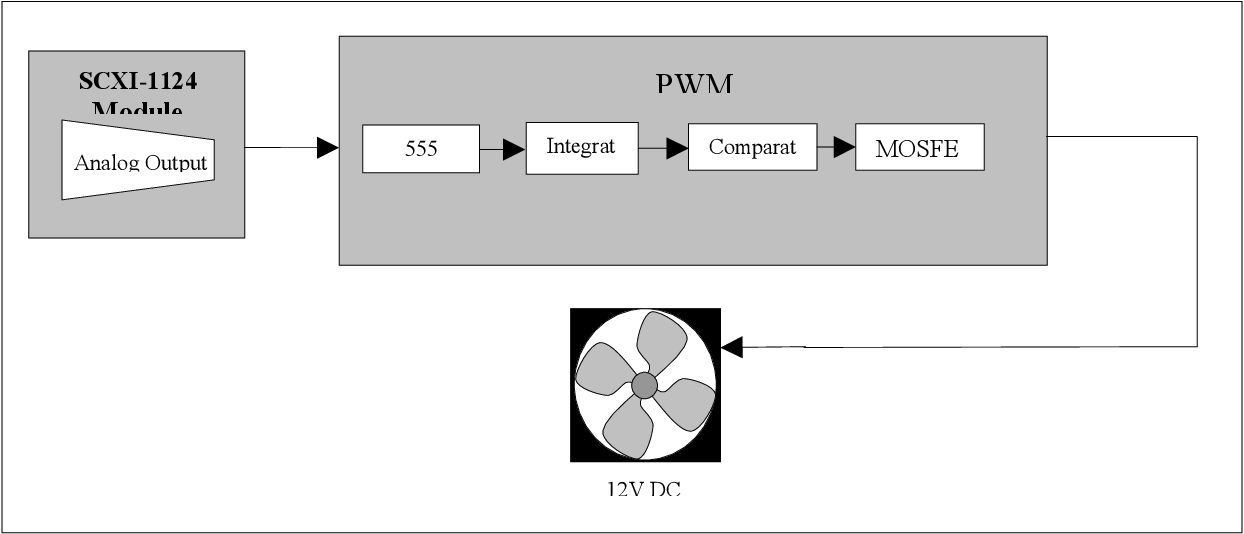
If (total_error >= max_control) total_error = max_control Įlse if (total_error = max_control) control_signal = max_control Įlse if (control_signal <= min_control) control_signal = min_control Total_error += error //accumalates the error - integral term Int delta_time = current_time - last_time //delta time interval Unsigned long current_time = millis() //returns the number of milliseconds passed since the Arduino started running the program PID_Control() //calls the PID function every T interval and outputs a control signal So here we have the PID controller algorithm written out on the Arduino ID. And thus we can adjust our control effort by simply increasing or decreasing this Kp constant. If our errors large, we’ll get a large control signal if our errors are small. It’s quite apparent why this is known as proportional control because with a fixed Kp constant the control signal is proportional to the error. Since all the P controller does is multiply the error by the control constant Kp. So let’s say we have a positive step change in the setpoint and therefore we get a positive error.
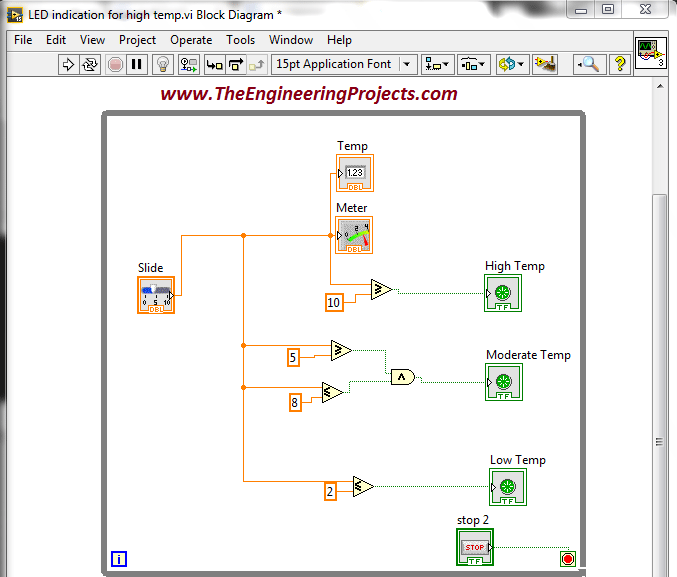
Now lets see how a closed loop system performs with just proportional control. But in order to understand the advantage and disadvantage of using one or more term, we will break down the controllers operation by dealing with each term separately. As you see in block diagram of PID controller, the error essentially goes through each PID block and their outputs are summed up and form a control signal that drives the process to the desired setpoint. Now I will discuss P or proportional term of the PID controller.
